Pre-terminated fiber assemblies are ideal for data center deployments because they enable high density, reduce labor and deployment time, and offer superior performance with less variability due to factory termination. However, not every fiber deployment is suited for pre-terminated solutions. Longer lead times, the need to carefully predetermine lengths, and higher material costs associated with pre-terminated solutions don’t necessarily make sense for low-count fiber deployments, disaster recovery, or other quick turn-around deployments. There are also specific applications and scenarios where field termination may be the only choice.
Fusion splicing is a field termination method that offers superior performance and is growing in popularity, and improvements in fusion splicing technologies now make it easier than ever to invest in this reliable termination method.
How Does Fusion Splicing Work in Fiber Optics?
Connecting two fibers via fusion splicing requires a fusion splicing machine that carefully aligns two cleaved fibers and fuses them via an electric arc. Splicing multi-fiber ribbon cable requires a mass fusion splicer that allows multiple fibers to be fused simultaneously. Fusion splicing is achieved with either fiber pigtails or splice-on connectors. Fiber pigtails feature a pre-polished, pre-terminated connector with a short fiber stub (usually 5 meters or less) fused to the connecting fiber. Splice-on connectors feature a pre-polished ferrule with a much shorter fiber stub that resides inside a connector. The fiber stub is fusion spliced to incoming fiber and the connector parts are assembled around the ferrule.
What Tools are Required for Fusion Splicing Fiber Optic Cables?
Fusion splicing machines use an electric arc that essentially melts the two fiber end faces and welds them together, maintaining an optimal path for the light signal. Early fusion splicing machines were large and expensive, costing upwards of $30,000, and the process often required multiple technicians and the need to qualify the quality of the splice using an OTDR. Over the past few decades, the cost of fusion splicers has decreased significantly with prices ranging from $3,000 for single-fiber fusion splicers to $12,000 for mass fusion splicers, making investment in this technology easy to justify.
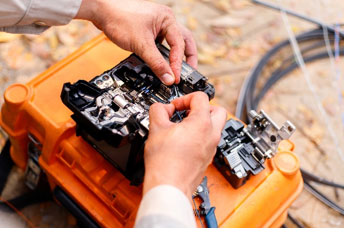
Today’s fusion splicers have become highly accurate through the use of cameras, magnification, and loss estimation technology that can evaluate the accuracy of the splice during the process. They are also more durable, portable, and easy for a single technician to operate with features like touchscreen monitors. Fusion splicing kits are also an option and contain everything a technician needs for virtually any splicing application.
There are generally two types of fusion splicers—clad alignment and core alignment. Clad alignment splicers align the outer edges of the fiber cladding, while core alignment aligns the core. Core alignment splicers are considered more accurate and carry a higher price, but modern-day clad alignment fusion splicers use an integrated camera and imaging technology to evaluate the accuracy of the splice. However, because today’s fiber manufacturers have improved the geometry of fiber over the past decade, a core alignment splicer should be used when splicing fiber from different eras since differences in fiber geometry can make cladding alignment more difficult.
When fusion splicing, it’s also important that both fiber ends are stripped and precisely cleaved. Rather than hand cleaving, it is recommended to use a quality cleaver with precision-engineered blades. Because small glass fragments are a safety hazard, cleavers should also have an integrated dust bin to collect fiber end cuts safely and automatically.
What are the Benefits of Fusion Splicing?
Fusion splicing is a more time-consuming deployment method compared to pre-terminated plug-and-play assemblies. However, it is an ideal option when link lengths can’t be predetermined or longer lead times are not an option. This makes it the termination method of choice for repairing fiber links. A fusion splice is also the strongest and most reliable permanent fiber connection, offering the lowest loss and least reflectance compared to other field termination methods. For example, splices typically have a loss of less than 0.1 dB while other termination methods typically yield a loss of 0.2dB or higher. This is especially a consideration in high-speed fiber networks with stringent insertion loss requirements. Note that a fusion splice is not the same as a mechanical splice where fibers are typically held together via index-matching gel. Mechanical splices are not as strong as fusion splices and have a higher loss than fusion splices, but they are ideal for emergency restoration.
Fusion splices can tolerate a wider storage temperature range, making it the termination method of choice in OSP FTTX deployments. Fusion splicing is also the de facto choice for terminating outside plant (OSP) 250-micron fiber to inside plant 900-micron fiber, so it is commonly used at the building entrance for transitioning from incoming service provider fiber.
With more affordable options, ease of use, and greater accuracy in fusion splicing, as well as the introduction of splice-on connectors, fiber splicing is becoming increasingly popular as a means for terminating fiber and meeting increasing bandwidth demands. Fiber splicing solutions achieve a fast return on investment as they enable technicians to seize more opportunities in today’s growing fiber market.
The good news is that Cables Plus offers a complete line of solutions to meet all your splicing needs, including fusion splicing machines, cleavers, strippers, fiber pigtails, splice-on connectors, protection sleeves, splice trays, and splice enclosures. Use the links below to explore our fiber splicing solutions or contact us for more information.
Shop Our Fiber Splicing Solutions Contact an Expert
Additional Resources: